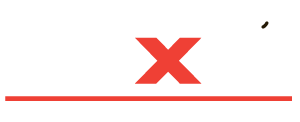
Maxoil Solutions Tackles Energy Industry Issues
25 Jun 2015
Maxoil Features in the June edition of Business Now; here is the article -
Efficiency, optimisation and integration. All three have become key focus areas within the oil and gas industry during one of the most testing periods in the sector’s long history.
For one global consultancy with its roots in Aberdeen, those three bywords also represent the focus of a strategy designed to tackle production issues worldwide.
Maxoil Solutions was founded in 2004 by Dr Wally Georgie and Mel Dow to bring together experienced consultants with a focus on operational expertise.
Both remain at the heart of the business, which has expanded from its Aberdeen roots to incorporate a base in Houston and a strong presence in Perth, Australia, and Stavanger in Norway as well as other key energy regions globally.
With expertise in a range of specialised process, engineering and production chemistry consultancy services, the Maxoil team’s ability to achieve process performance optimisation by applying effective knowledge to new projects and operating assets has presented new opportunities in the first quarter of 2015.
Maxoil Solutions managing director Mel Dow is well versed in the cycles of the energy industry but believes the current situation presents a unique chance to embrace solutions which will have a lasting impact.
He said: “The impact of the reduction in the oil price has been significant and there is no escape from that. It is imperative in the long term that we see that trend reversed, but in the short term there are challenges which must be faced.
“The overarching theme is in improving efficiency, increasing uptime and minimising OPEX in every aspect of operations and that should be viewed as a positive exercise. Maxoil has been built on the foundations of using its expertise to optimise production performance, so we have entered this period ahead of the pack in many respects.”
Maxoil has specialist areas of expertise in operations assurance, flow assurance, fluids separation, produced water management, sand and solids management, gas treatment and transport, chemical treatments and contaminants, process troubleshooting, advanced diagnostics, de-bottlenecking and technical awareness training.
Mel Dow added: “A holistic approach is at the heart of what we do, blending our core disciplines of process engineering and production chemistry with hands-on operations experience. The end result is a single consultancy designed to tackle the issues that hurt our clients - whether they be downtime, performance, environmental or financial.
“The approach has helped build the business over the past 10 years and will be key as we look to the future. We have a strong and comprehensive team in place, ready to respond to the twists and turns in the road ahead. Optimising asset performance through expertise and innovation continues to be the goal.”
Demand for lifecycle solutions is not confined to the North Sea, with Maxoil’s knowledge and experience being tested in all key production regions. The team’s input spans well sampling, fluid characterisation and concept development for discoveries through to subsea commissioning, operations troubleshooting and late-life performance improvement strategies.
A growing range of services has supported the company’s development and there is a clear strategy for its continued evolution.
Mel Dow said: “We view integration as a tremendously powerful tool for our clients, particularly in driving production efficiency. Chemistry issues are something every production facility will experience, whether in reservoirs, flowlines or topside equipment. In our experience the common denominator is often too little production chemistry input at the Front End Engineering Design (FEED) stage and we are working closely with clients to ensure early integration.
“By promoting awareness and changing priorities, as well as placing an emphasis on ensuring adequate and representative fluid samples are being taken, there can be a tremendous impact on Life of Field production performance.”
Issues including souring, scaling, emulsions, foaming, solids deposits and waxing are among those being tackled by Maxoil on a daily basis.
The Maxoil managing director added: “Fully integrating production chemistry into the basis of design for each project is vital and can ensure ‘surprises’ are avoided. On many projects a silo mentality can develop between disciplines where the importance of one input to the project is not realised by the rest of the team.
“Whilst this applies at the FEED stage, integration is also important for projects relating to operating assets. Only a joined up approach can provide the problem solving which will be the bedrock for a positive production future.”