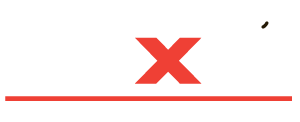
New Thinking on Produced Water Treatment System Design Review
17 Sep 2013
By Donal Ratcliffe, Production Chemistry Consultant, Maxoil Solutions
In the production of crude oil the treatment and disposal of produced water has traditionally been considered as an afterthought: for most fields produced water production at start-up is low therefore the installed treatment system copes well. As the field matures, produced water production increases and fluid properties change. As a result maintaining acceptable discharge and disposal limits becomes more challenging. Operators resort to reactionary “quick-fix” solutions to produced water treatment problems targeting what appears to be the source of a problem. Maxoil’s experience is that produced water treatment problems are complex, deep seated and encompass the complete processing system starting with the primary crude oil separators. Solving produced water problems requires a systematic, analytical approach.
Identify the Root Cause of the Problem
Produced water treatment systems comprise of a series of inter-connected processes with the performance of each component depending on the performance of the upstream system, starting with the primary crude oil separator. If the primary separator cannot achieve satisfactory produced water quality and uniform flow the downstream system will be severely compromised. To understand how the system is performing it is necessary to use a systematic problem-solving approach beginning with data gathering. From this information the root cause of poor performance can be identified. Areas for investigation can include:
- Well configurations and characterisations
- Compositional and physical fluid analysis of water, oil and gas
- Operational and reservoir conditions
- Operational and training procedures
- Maintenance philosophy and records
- Production chemistry and solids monitoring
- Production chemical injection strategy
- Process Vessel internals and controls
Holistic Analysis
Once the data is collected and reviewed a full-scale holistic mapping of the system is performed, starting with the most upstream end of the system, to identify all potential contributing factors to a problem. This process includes field surveys and trials, chemical and engineering modelling, operator interviews and workshop sessions, equipment and technology reviews, historical mapping plus laboratory analysis of samples to build up a comprehensive picture of system performance. Once the complete system operation and performance characteristic is understood the root cause of a problem can be identified.
Typically produced water problems are caused by poor equipment and system cleanliness (or “hygiene”) plus poor understanding of current and future system conditions. This can be created by a combination of issues covering: ineffective chemical injection strategy, poor solids management, poor equipment design and maintenance, inefficient system control, inadequate training and ineffective monitoring and analysis.
Implementing a Remedial Programme
Once the root cause of poor system performance has been identified a remedial programme for equipment and system performance improvement can be planned and initiated. This can include additional investigation to consider such aspects as debottlenecking, throughput upgrade and separation performance improvement. Subjects covered by a remedial programme can include:
- Upgrading operational and training procedures
- Slug flow control
- Optimising chemical treatment strategy
- Improving production chemistry management (emulsions, solids, corrosion, chemical compatibility)
- System monitoring regime upgrade
- System pressure and temperature optimisation
- Vessel internals, residence and flow optimisation
- Pipework and valve configuration optimisation
- System control parameter upgrades
- System maintenance scheduling