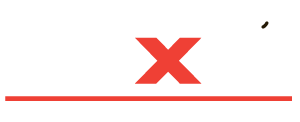
Heavy Oil Characterisation Identifies Flow Assurance Risks that Drive System Designs
1 Oct 2013
By Colin Smith, Production Chemistry Consultant, Maxoil Solutions.
The necessity for accurate characterisation of heavy oil separation properties and emulsion formation tendency is critical for any design team as it has a major impact on the field development concept selection, including, for example, the fluid lifting mechanism for production wells, on the system detailed design and finally on the selection of fit for purpose operational solutions, especially for offshore new field developments.
Heavy and extra heavy oil are crude oils which are so viscous that they will not flow easily (see the image of a viscous heavy oil below) and for this article heavy oil is referred to as oil with an API gravity of less than 23o, noting that classification schemes exist that delineate such oils into medium heavy, heavy, extra heavy and bitumen oils, based on density and dynamic viscosity.
As oil and gas resources in current basins of the world continue to decline, heavy oil provides a significant solution to the world’s thirst for energy. There are enormous reserves of heavy oil, with potential reserves of up to 1,000,000 billion barrels, depending upon the recovery factor but current technologies only recover low amounts of the in-situ hydrocarbon and so far < 1% has been produced or is under development. If oil and gas companies could recover 50% of the available deposits, 50% of North American demand would be met for more than 50 years.
There are numerous flow assurance challenges associated with the production and processing of heavy and extra heavy oils in both onshore and offshore environments that directly impact the ability of any process system design to successfully handle such fluids. Many of these challenges are centred on the production separation system and are generally addressed in the early stage of the field development. These challenges include the following:
- Artificial lift options (gas lift, ESPs, HSPs, etc.)
- Space and weight restrictions on platforms and FPSOs in part govern separation vessels sizes and residence times
- Accuracy of the fluid characterisation data for the Basis of Design (BOD).
- Heating and power requirements
- Internal design of the separation vessels
- Process vessels configuration
- Oil, water, emulsion, foam, microbiology and solids handling
- Optimal treatment chemicals application
A critical aspect of the heavy oil production separation system design is the accuracy of the fluid characterization data upon which the design is based. During the appraisal phase of a new heavy oil field development, when appraisal well tests occur and fluid samples are being collected for other issues such as PVT studies, it is paramount that good quality representative samples of oil (and indeed formation water) be collected, so that some samples be allocated for the accurate determination of fluid physical properties and production chemistry characteristics, as this is crucial information for any production and separation system basis of design (BOD). The degree of drilling mud contamination (especially if oil-based mud, OBM) is also very important to know also.
It is recommended that both live downhole and stabilized oil samples be collected and analyzed with one of the more important heavy oil parameters required being the dynamic viscosity of the oil and its water-in-oil emulsion. Defining the factor between dry oil and emulsion viscosity for a system is a key Flow Assurance parameter input for any system design. Of course it is crucial that not only are representative fluid samples required but the laboratory test methods selected to define the rheological properties and to characterize the Production Chemistry issues must also be fit for purpose for each system. An example of this is the measurement of fluid dynamic viscosity where the test shear conditions must directly relate to the passage of live fluids through the points of significant shearing, i.e. shearing due to passage through electrical submersible pumps (ESPs) or hydraulic submersible pumps (HSPs) and with gas lift and on passage of fluids through wellhead choke valves. An example sample of heavy oil emulsion is show below. Calculation of representative flow regime and shear conditions for emulsion creation in the laboratory is recommended or the measured properties used for design purposes will be misleading and can lead to later unnecessary production equipment redesign and upgrades.
Following the laboratory measurement of rheological properties, it is then possible to model live fluid viscosities using PVT software and viscosity correlations, including algorithms to calculate relative viscosity, the ratio of emulsion viscosity to stabilized crude oil viscosity. Heavy and extra heavy oils can exhibit unusual rheological properties and variable Flow Assurance characteristics during production and processing, which must be properly defined and these include but are not limited to the following, which must be considered in any new facility design:
Variable multiphase flow and slugging characteristics in surface and subsea pipelines that needs to be modelled:
- High oil dynamic viscosities causing lifting issues in production wells which influences lifting mechanism selection, especially in remote offshore locations with subsea wells.
- For subsea systems with long tieback flowlines, problems with high viscosity fluids requiring relatively high restart pressures following lengthy unplanned shutdowns.
- Variable tendencies of oil types to form stable emulsions, including differing amounts of emulsifying agents.
- High emulsion viscosities especially up to a critical maximum prior to the emulsion inversion point.
- Onerously slow oil-water separation rates linked to typically low oil-water density contrasts and high continuous oil phase viscosities, unless the fluids are heated to 120 oC or more to lower the fluid viscosities.
- Swelling of the continuous oil phase by flashed gas causing gas under-carry downstream.
- Stable foam formation in separators and slug catchers that cause liquid carry over to the gas treatment system.
- Heavy oils with associated formation derived sand and fines solids production can further stabilize emulsions and drop out subsea and in topsides vessels to plug and erode internals and to reduce vessel residence times.
- Varying propensity to form precipitated solids from the production fluids during production and de-pressurisation while flowing to the surface, which can generate various unwanted solids that form flow restrictions and even plug lines.
Some case studies to illustrate these points follow here:
Case Study 1: Offshore Western Australia
Offshore production of heavy oils of between 17 to 20o API gravity to an FPSO with common production facilities in an environmentally sensitive area, requiring good performance of primary separation vessels as being vital in ensuring standards were met for produced water discharge quality in addition to export oil quality. A site study was carried out to review the proposed designs of production vessels in the system, covering all aspects of vessel designs that would affect performance.
Discoveries were made on-site with recommendations implemented by the Operator that led to an optimised separation system design including:
- Key emulsion stabilisers were found to be carboxylate soaps, so demulsifiers could be reformulated to handle such components and improve performance.
- Separator vessel internals were redesigned to improve performance.
- An optimal emulsion treating temperature of 60 oC was identified and set in the design.
- Hot water recycle to 1st separator inlet was incorporated to aid separation.
- A revised subsea and topsides chemical application strategy was implemented.
- New operational practises were put in place to handle fluids from newly drilled flow-back to host production wells including optimised use of the slops tank.
Case Study 2: Onshore Alaska
A heavy oil central process facility (CPF) was faced with emulsion handling problems and sand management issues that combined to give poor performance in the surface separation facilities. The loss of fluid quality control resulted in off specification export oil and oil-in-water losses of about 600 bpd, equating to 1 million USD/month losses. The cost of ‘band aid’ type solutions, such as installing hydrocyclones, were high at 50 million USD which was unattractive and it did not address the underlying operability issues. It was a fact that the range of different types of produced fluids to this production facility were not fully understood in terms of the Flow Assurance risks and Production Chemistry characteristics.
A series of on-site studies were undertaken to fully understand the fluid chemistry and properties, to define the Flow Assurance problems and to evaluate the performance of the process facilities equipment. An on-site fluid quality survey was undertaken, samples were collected with separation characteristics and emulsion stability evaluations carried out, including identification of emulsifying agents, such as soaps. Process diagnostic surveys were carried out across separation vessels, e.g. see the inlet separator below, engineering design tools were employed for hydraulic analysis and residence time assessments and chemistry simulation programs, like ScaleChem were employed to assess the impact of scale solids on emulsion stabilisation.
All the consultancy work culminated in a cost-effective holistic solution for this series of interrelated problems whose overall cost was less than 20 million USD and it included resolution of the inherent operability issues. The solutions included upgraded separator internals, redesigned settling tanks, improved sand removal systems operation, improved chemical treatment of emulsions, updated operational practises and the separation strategy was changed to make it fit for purpose for heavy oils handling.